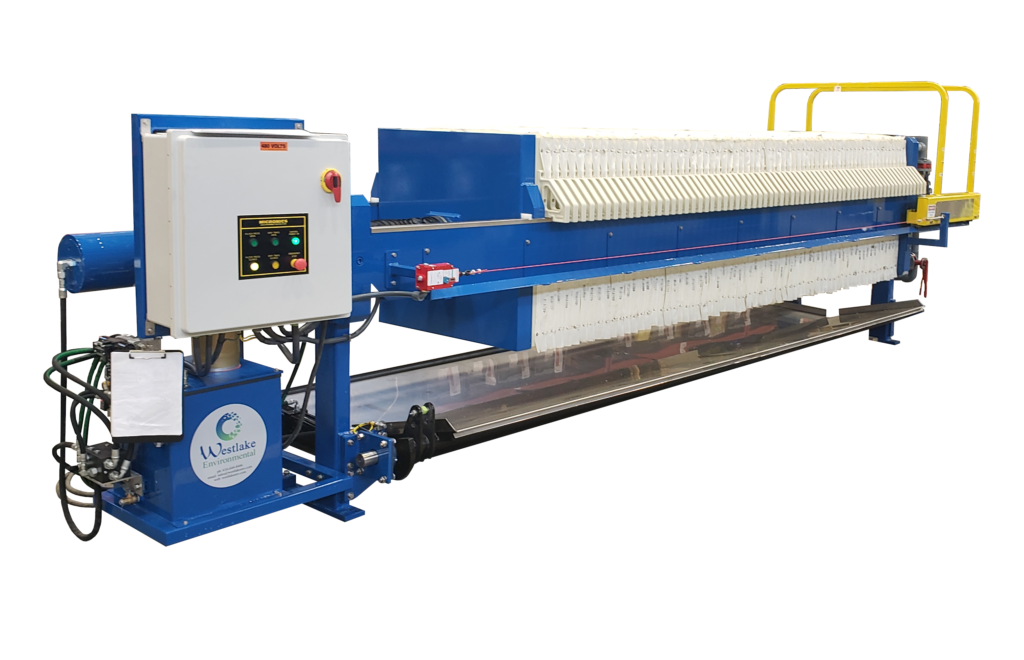
WHAT IS A FILTER PRESS AND HOW DOES IT WORK
The Westlake Environmental Filter Press (FP) is a fixed volume, batch pressure filter that separates liquids and solids. A set of filter plates with clothes are sandwiched together in series. Once the plates are compressed together hydraulically, sludge is pumped into the center of the filter plates with all chambers being filled simultaneously. The solids are retained on the filter clothes, which act as a depth filter for liquid/solid separation, while clean fluid (Filtrate) travels thru to the discharge manifold and exits the press. When the filter plates are full, the cycle is complete, and the filter press is opened to discharge the solids off each plate.
WHAT’S INVOLVED
The filter press consists of a head and follower that contain a series of plates that are supported by side bars or overhead beams. The head serves as a fixed end to which the feed and filtrate pipes are connected. The follower moves along the side bars and presses the plates together during the filtration cycle by a hydraulic or mechanical mechanism. Each plate includes filter cloth on both sides and, once pressed together, they form a series of chambers. The plates have a centered feed port that passes through the entire length of the filter press so that all the chambers of the plate pack are connected together. Likewise, four corner ports connect all the plates and collect the filtrate in a “closed discharge” towards outlets that are located on the same side as the feed inlet.
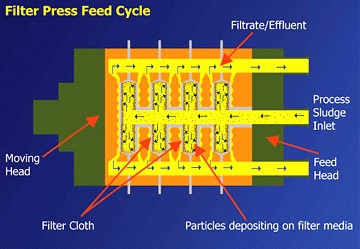
Contact Westlake Environmental for more information at 616-610-1450 or at sales@westlakeenv.com.