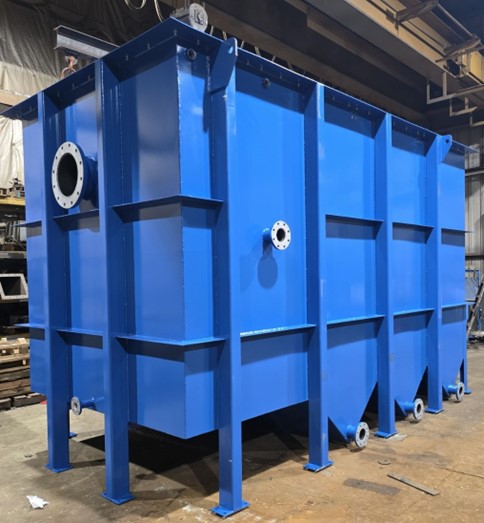
A large OWS ready to ship. The Separator does an extremely efficient job in removing Fats, Oils and Grease (FOG) from a waste stream. Built in A-36 carbon steel with a robust interior/exterior coating system.
A large OWS ready to ship. The Separator does an extremely efficient job in removing Fats, Oils and Grease (FOG) from a waste stream. Built in A-36 carbon steel with a robust interior/exterior coating system.
An Inclined Plate Clarifier and a Chemical Addition System ready to ship. The Chemical Addition System pre-treats the water to create a large floc particle, which enhances solids removal by the Inclined Plate Clarifier. Both tanks are built in A-36 carbon steel with a robust interior/exterior coating system.
An Oil Water Separator ready to ship. The Separator does an extremely efficient job in removing Fats, Oils and Grease (FOG) from a waste stream. Built in A-36 carbon steel with a robust interior/exterior coating system.
An Oil Water Separator ready to ship. The Separator does an extremely efficient job in removing Fats, Oils and Grease (FOG) from a waste stream. Built in A-36 carbon steel with a robust interior/exterior coating system.
Two more Oil Water Separators in the fabrication process. Before completion tanks will receive continuous welds inside and out as well as a robust interior/exterior coating system.
An Emulsion Cracking System ready to ship to a customer dealing with emulsified oils in their waste stream. All Westlake Environmental equipment ships complete, pre-tested and ready for installation. Tank is manufactured in 304 stainless steel material and includes:
A filter press ready to ship. Customer has an existing Inclined Plate Clarifier (IPC) that requires dewatering of the produced sludge, which a filter press accomplishes very efficiently. Filter press includes:
An Oil Water Separator ready to ship. Tank is manufactured in A-36 carbon steel material with a robust interior and exterior coating system. Tank arrives at customer location complete and ready for installation. Tank includes:
Two more Emulsion Cracking Systems ready to ship. The same customer has purchased many of these same tank designs as they find the systems easy to operate with minimal maintenance. Tanks arrive at customers location complete and ready for installation. Tanks are manufactured in 304 stainless steel material and include:
An additional six (6) Inclined Plate Clarifiers shipping to the same customer!
Customer has purchased this same style tank in the past, and continues to purchase this style because of the robust design and ease of maintenance. All Westlake Environmental equipment ships complete, pre-tested and ready for installation. These particular tanks are manufactured in 316 stainless steel material and include an interior/exterior coating system per customer’s request.